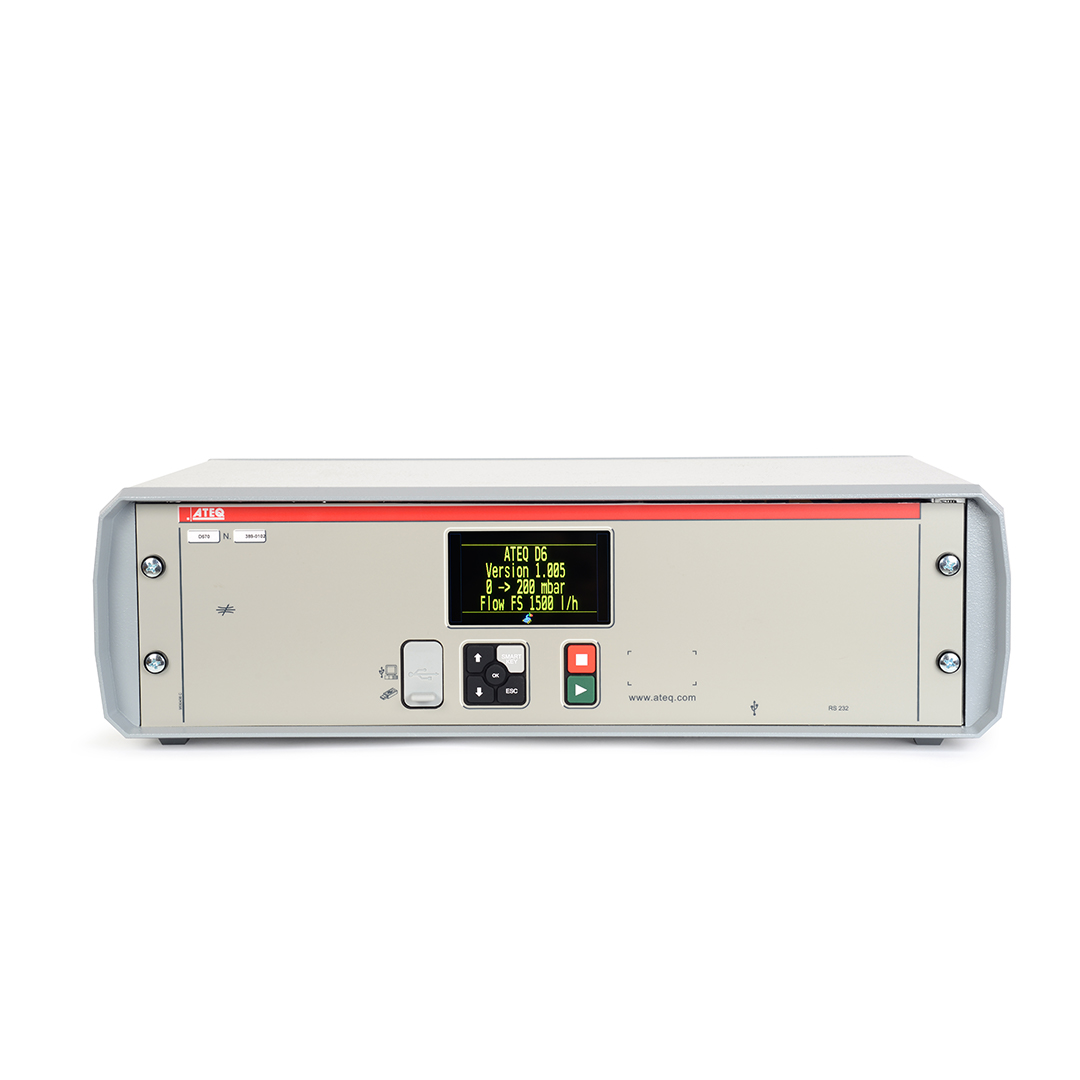
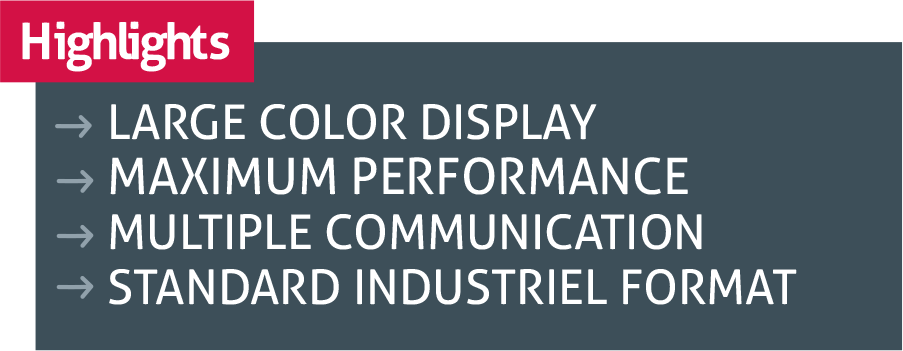
D670
HIGH SPEED FLOW TESTER FOR PRODUCTION LINES
ATEQ presents its revolutionary flow tester: D670.
New electronic module, new measurement module, new interface, new accessories… All has been made to improve your quality control.
And yet, inside can be found the latest leak testing technics and technology that will guaranteed you the fastest and most accurate leak testing cycle on the market.
D670: APPLICATIONS
D670 : FEATURES
- Flow measurement in direct or indirect testing
- Continuous measuring mode
- Wide flow measurement range
- USA, S.I. and customer units
- Measurement in standard or customized conditions
- Recalculated flow at the nominal pressure
- Measurement element fully integrated into one module
- 128 programs
- Mechanical or electronic regulator from vacuum to 10 bar
- Setting on line (via USB)
- 2 languages (English + other one)
- Manual calibration on front panel with calibrated leak
- Data storage on internal memory or USB key
ENVIRONMENT :
ROHS standard
FLEXIBLE COMMUNICATION FORMAT :
- RS232: Printer, modbus RTU
- Slave USB: PC supervision (WinAteq 300, sesame)
- Master USB: USB key to transfer (parameters, results, …)
- Option Fieldbus: Profibus, devicenet, profinet, Ethernet/IP, Modbus RTU
D670 : SPECIFICATIONS
D670 : OPTIONS
- 9 inputs / 5 local outputs compatible with 5 series instruments
- 6 inputs/ 6 outputs 24 V programmable for external automation
- External capillary: closed to test port
- Electronic regulator
- Dual pressure
- Automatic calibration check
- Shut off / dumping / by-pass valve
- 2 pneumatic outputs for control of sealing connectors
- Memory card for archiving results (400 000)
D670 : TECHNOLOGY
Sometimes a leak can be considered as a “small flow”, or a flow as a “big leak”. When your reject level is too high for other technologies, it may be necessary to use a laminar flow tester. A flow takes place between the pressure line and the leak hole of the part.
Our instrument features a laminar flow element across which our differential pressure transducer is connected.
Every flow generates a pressure difference between the inlet and outlet of the laminar flow element, and this variation is measured by the pressure transducer.
When the fluid (gas) enters the device 1, it moves through a calibrated flow tube 2 which causes a drop in pressure. The pressure drop is measured by a differential pressure sensor 3. The pressure of the part under test 5 is measured by the sensor 4.
D670 : DOCUMENTATION