E-MOBILITY LEAK TEST
ATEQ has a variety of methods to leak test batteries throughout the production process. Leak testing electrical vehicle battery cells, for example, begins with an ionic leak test of the battery cell pouch and ends with pressure leak testing the entire battery tray.
In e-mobility applications, ensuring the integrity of various components through comprehensive leak testing is crucial for the reliable and safe operation of electric and hybrid vehicles.
- Battery Packs: Battery enclosures in electric vehicles house lithium-ion cells that store energy for propulsion. Leak testing these packs is vital to prevent electrolyte leakage, which not only compromises the battery’s performance but also poses safety risks such as thermal runaway or fire hazards.Every sub element of the battery pack should be also leak testes such as: cells, modules, tray ect…
- Cooling Systems: Electric vehicles rely on cooling systems to maintain optimal operating temperatures for batteries, motors, and power electronics. Leak testing coolant circuits and connections helps identify potential leaks that could lead to system inefficiencies, overheating, or even component damage.
- Fuel Cell Systems: In hydrogen fuel cell vehicles, leak testing is essential for ensuring the integrity of hydrogen storage tanks, fuel cell stacks, and associated plumbing. Detecting leaks in these systems helps prevent hydrogen loss, maintains fuel efficiency, and mitigates safety risks associated with hydrogen leaks.
- HVAC Systems: Heating, ventilation, and air conditioning (HVAC) systems play a crucial role in ensuring passenger comfort and safety. Leak testing HVAC components such as evaporators, condensers, and refrigerant lines helps maintain system efficiency, prevents refrigerant leaks, and ensures optimal cabin climate control.
- Charging Systems: Electric vehicle charging infrastructure, including charging cables, connectors, and seals, must undergo rigorous leak testing to ensure safe and reliable operation. Detecting leaks in charging systems helps prevent electrical hazards, ensures efficient energy transfer, and maintains the integrity of the charging infrastructure.
- Powertrain Components: Electric motors, inverters, and power electronics are integral to the operation of electric vehicles. Leak testing seals and connections in these powertrain components helps prevent fluid leaks, such as coolant or lubricants, which could lead to performance degradation, system malfunctions, or even catastrophic failures.
- Hydraulic Systems: In hybrid vehicles or those equipped with hydraulic components, leak testing hydraulic circuits is essential for maintaining system efficiency and reliability. Identifying and repairing leaks in hydraulic systems prevent fluid loss, ensures proper component operation, and extends the lifespan of hydraulic components.
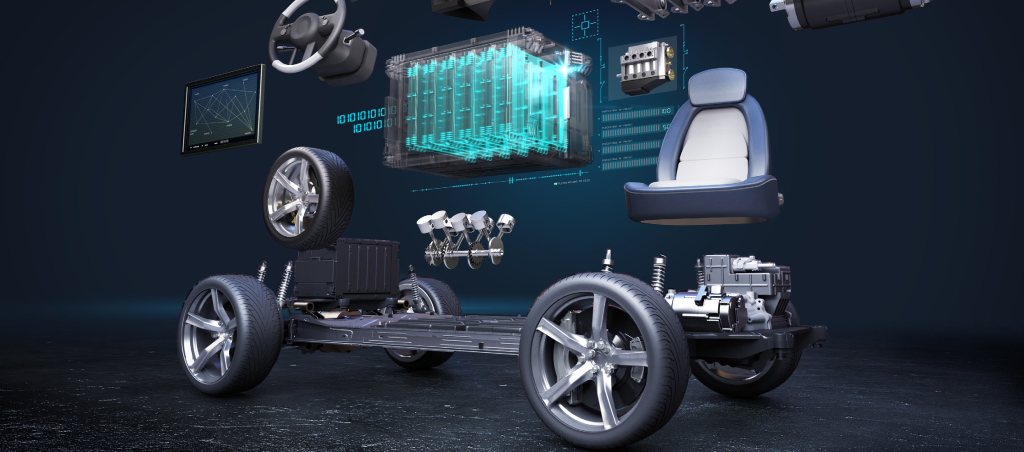
How can ATEQ support those mutations of the markets?
ATEQ supports the OEM industries by proposing new solutions for leak testing the specific elements such as: battery (tray, cell, module) cooling circuit, inverter, guidance systems… For this new market, battery leak testing is essential for electric vehicles, for battery packs any leakage can compromise safety, performance, and longevity of the system. One of the solutions developed by ATEQ Group for answering easily to the EV market regulations is the combination of the DNC technology described below and the large volume tester called F670LV.
Differential Noise Cancelling (DNC) is an innovative technology developed by ATEQ for leak testing applications, particularly in the automotive industry. DNC is designed to enhance the accuracy and reliability of leak testing systems by minimizing the impact of background noise and external factors on test results. In leak testing applications, background noise, such as atmospheric air movement, machinery, or ambient environmental conditions, can interfere with the accuracy of the test results. DNC technology aims to mitigate this interference by analysing and cancelling out this “background noise”, thereby improving the sensitivity and reliability of the leak detection systems.
This DNC technology is used, combined with the F670-LV device. It is a breakthrough instrument able to leak test very large volumes using a new patented technology (based on pressure decay) thanks to the high sensitivity of our latest pressure transducer. By using ATEQ’s F670LV Differential Pressure Decay leak Tester with DNC, it is now possible to detect accurately pressure drops below 0.1 Pa/sec (equivalent to 1/100 mm water gauge pressure change in 1 second).
For battery leak testing of the cell, ATEQ presents the new patented B28 testing method which offers a safe low ionization voltage to ionize oxygen molecules in the air around the battery cell. If the battery cell is properly insulated, the instrument will show a 100% reading. If there is a leak in the battery insulation, ionized oxygen molecules will be able to flow through the hole and the ions will connect to the inside of the battery cell, without igniting it. This will show a 0% insulation percentage reading on the instrument and the operator or machine can then reject the part.
The B28 can be automated into a production line to support fast pass/fail testing of the cell. The faulty part could then be taken to a rework bench for manual leak localization testing by using the Ioniq wand to find where on the cell the testing needle creates a zero percent reading on the instrument.
After the battery cells pass the ionization leak test, the next phases are putting several cells together to create a battery module, combining the modules into a battery pack then putting several battery packs together into a battery tray. Each of these battery packages requires leak testing. Leak testing battery modules, packs or trays involves a different type of leak testing than the cells. ATEQ differential pressure decay leak testers, like the F620, can test the battery packaging by sealing off the packaging openings and injecting the package with compressed air, measuring the pressure and measuring how much the pressure drops, which would signify a leaking battery pack. If the leak rate is within testing specifications, the battery packaging is airtight.
ATEQ accompanies its customers in their production and assembly process of batteries for electric vehicles.
We manufacture and supply the equipment that allows you to perform all the tests you need, such as :
- Connection of the battery cells
- Modularisation
- Assembly of the pack,
- Application of the battery management system (BMS)
- Battery charging.
We also provide monitoring, training, calibration, maintenance and troubleshooting of the installed equipment.
“Ateq is dedicated to your long-term success”